슈리 플라스틱 작은 알모양으로 하기 선 PP, PE, LDPE, HDPE, PVC 등을 분쇄, 세척 및 펠릿화하여 귀중한 플라스틱 펠릿으로 재활용합니다. 처리능력은 100~500kg/h이다.
당사의 플라스틱 재활용 라인은 PS, ABS, PA 등 다양한 플라스틱 폐기물을 처리할 수 있습니다. 그것은 고효율, 좋은 성능 및 비용 효율성의 특징을 가지고 있습니다.
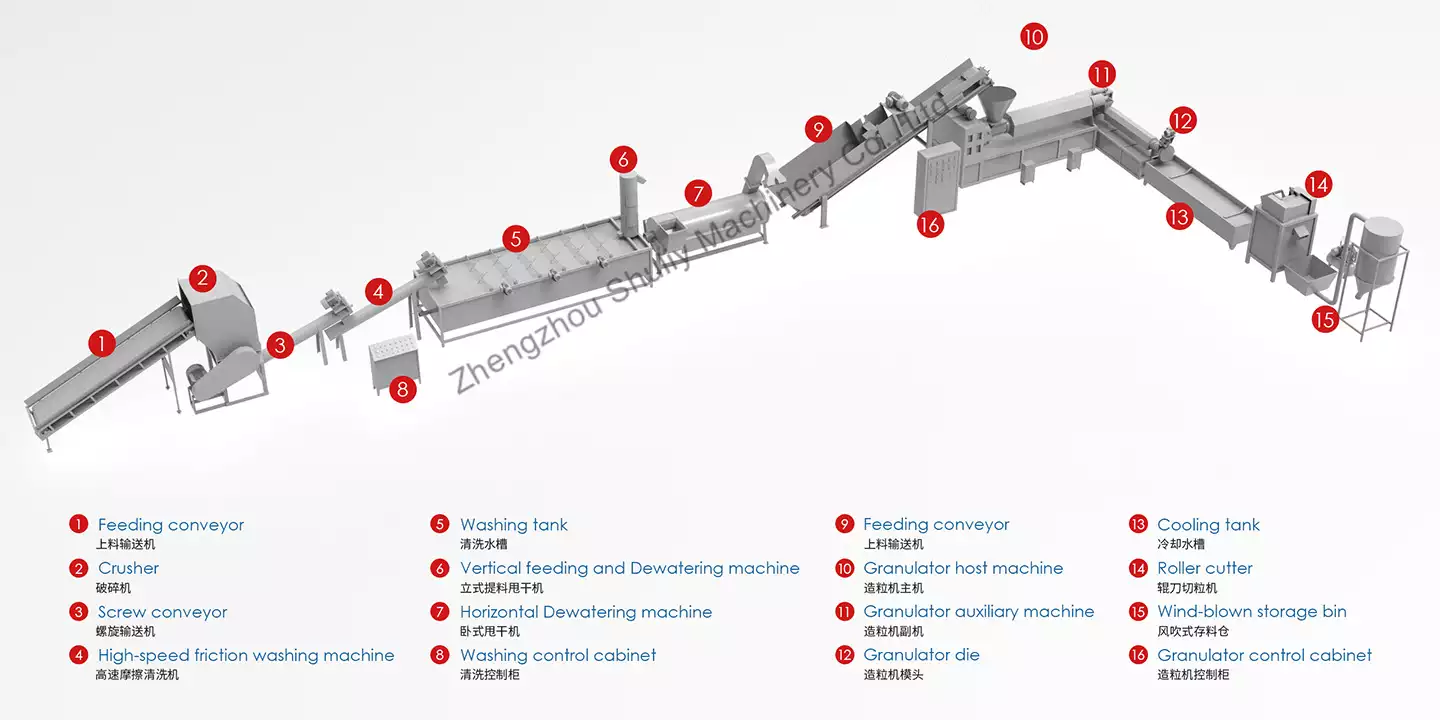
Shuliy 플라스틱 재활용 펠릿화 라인은 에티오피아, 모잠비크, 가나, 나이지리아 등으로 수출되었습니다. 이는 고객이 폐기물 재사용 및 수익을 달성하는 데 도움이 됩니다. 따라서 이 PP PE 플라스틱 세척 펠릿화 라인은 폐플라스틱 재활용 공장에 이상적입니다.
플라스틱 재활용 기계 라인에 대한 비디오
PP PE PVC 플라스틱 과립 제조용 원료
이 플라스틱 재활용 라인을 이용해 수익을 창출하려면 먼저 어떤 플라스틱을 재활용할 수 있는지 이해해야 합니다.
원료는 다음과 같습니다:
PP, PE, LDPE, HDPE, PS, ABS, PA, PVC, PC, POM, EVA, LCP, PET, PMMA, 플라스틱 욕조, 족탕, 버킷, 플라스틱 의자 및 스툴, 비닐봉지, 쓰레기 봉투, 짠 가방, 포장 스트립, PP 주스 병, 샴푸 병, 농업용 필름, 식품 포장 필름, 온실 필름, 빈 용기, 튜브, 포장 스트립, 로프 및 케이블, 어망 및 직조 섬유, 등.
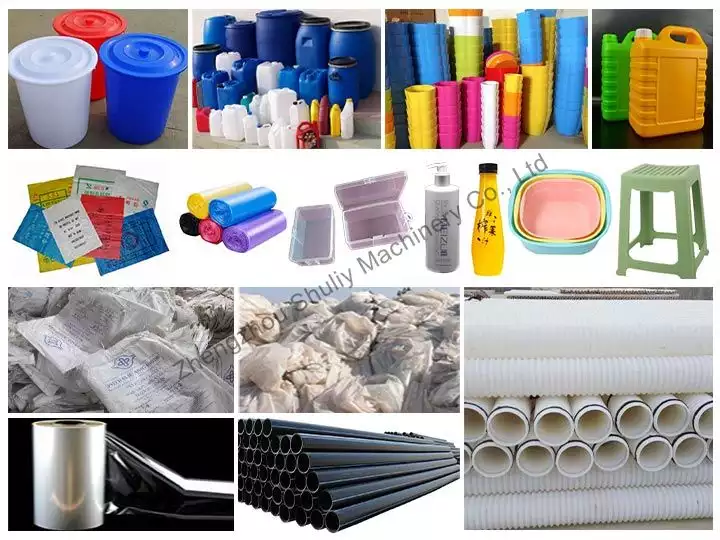
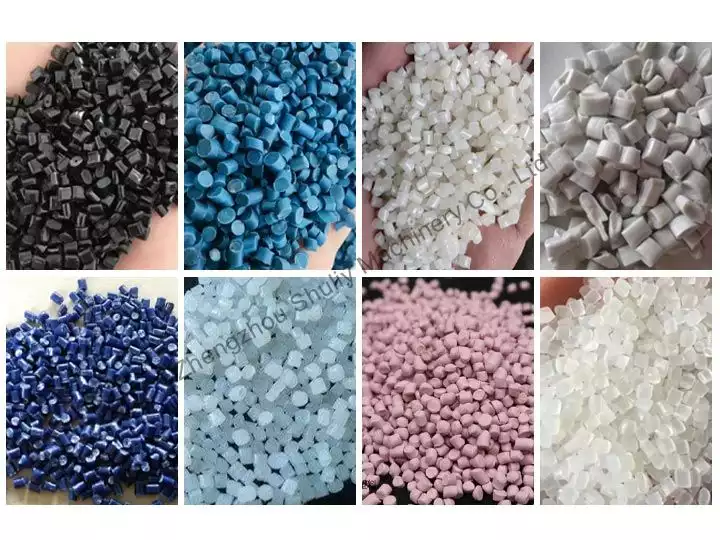
플라스틱 펠릿화 공정은 어떻습니까?
원재료를 알면서 플라스틱을 플라스틱 펠릿으로 바꾸는 단계와 그 과정에 사용되는 장비를 소개합니다.
주요 단계는 다음과 같습니다 파쇄→세척→건조→펠릿화→절단. 자세한 내용을 함께 살펴보겠습니다.
눌러 터뜨리는
먼저, 플라스틱 분쇄기 기계 폐플라스틱을 작은 입자로 분쇄하는 것입니다. 일반적으로 하나의 컨베이어 벨트에는 편리한 플라스틱 재활용을 위해 플라스틱 분쇄기가 장착되어 있습니다.
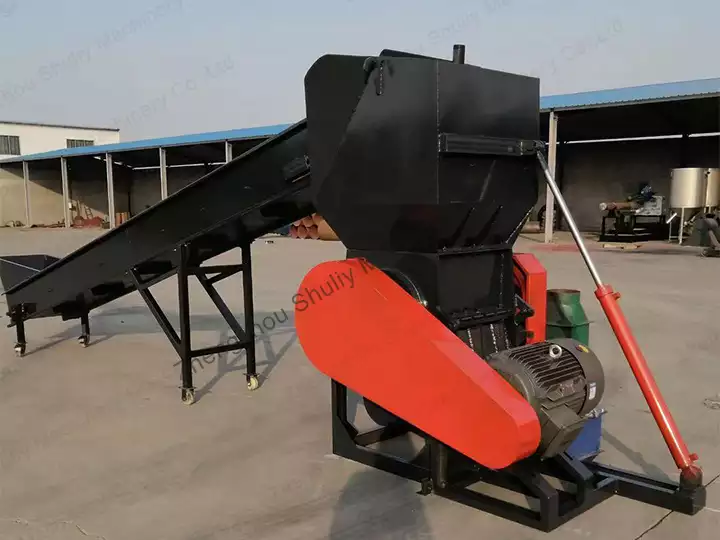
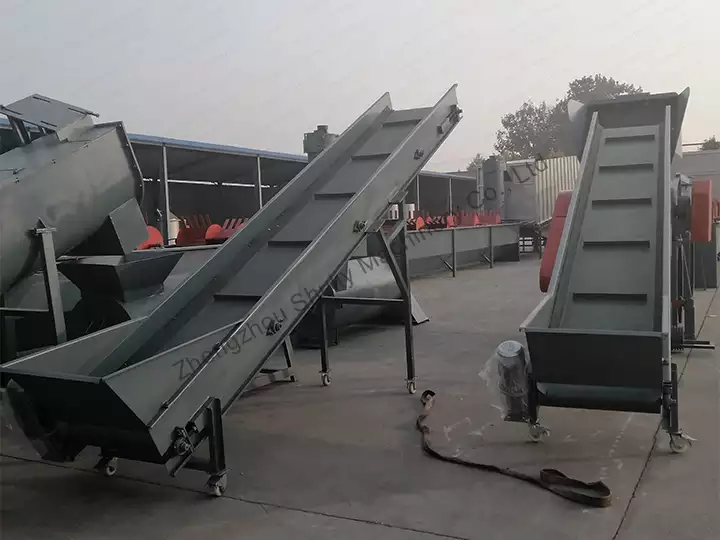
- 기계 이름: 플라스틱 분쇄기
- 용량: 400-1200kg/h
- 블레이드 소재: 60Si2Mn, 5Sicr
- 화면 크기: 필름용 40-50mm, 강성용 20-26mm
- 선택적 전원: 전기모터, 디젤엔진
- 장치 선택: 부채와 샤프너
- 필름재 분쇄용 팬
- 20톤의 원료 처리가 가능한 샤프너
- 기계 이름: 컨베이어
- 용량:1000-1200kg/h
- 힘: 3kw
- 길이: 5m(맞춤형)
- 너비: 0.8m
세탁
파쇄한 후 사용해야 합니다. 플라스틱 세탁기 표면 오염 물질, 그리스 및 기타 불순물을 제거합니다.
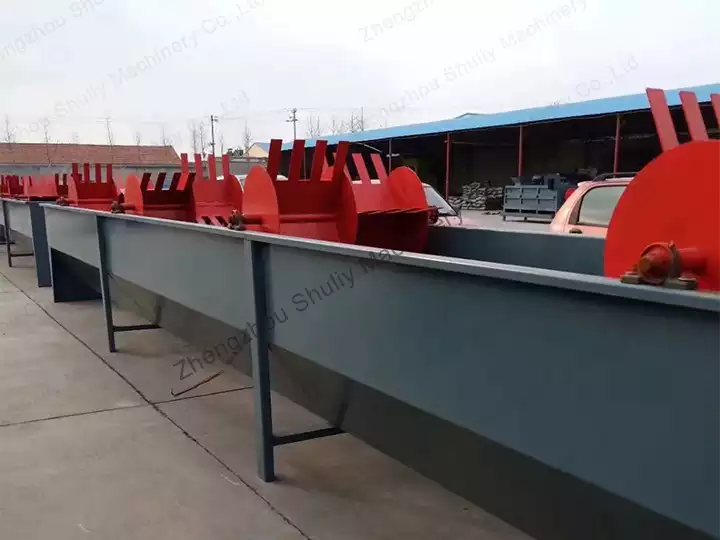
- 표준 길이: 6-10 패들 기어 사용 시 15-20m
- 최소 구성: 패들기어 2개로 5m
건조
수분을 제거하려면, 탈수기 필요합니다. 우리는 수직 및 수평 건조기를 모두 제공한다는 점에 유의하는 것이 중요합니다.
- 필름재료 수직건조기
- 단단한 재료용 수평 건조기
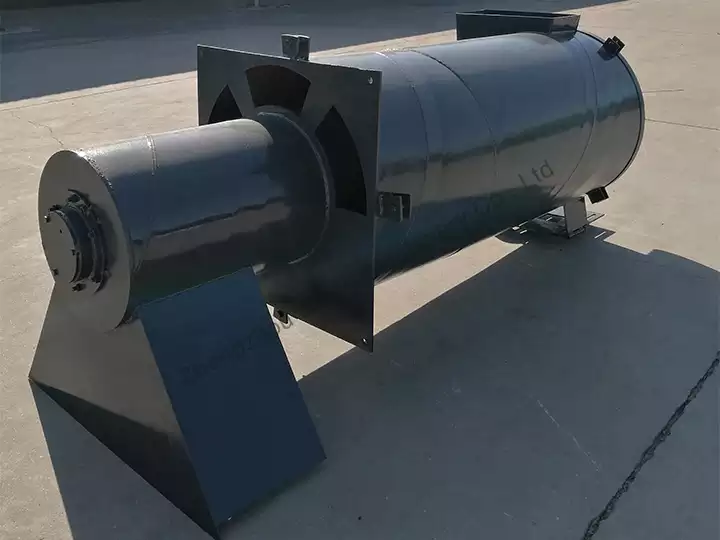
펠렛화
다음으로 가장 중요한 단계인 과립화입니다. 그만큼 플라스틱 펠렛타이저 건조된 플라스틱 PP PE 플레이크를 가열, 용융 및 압출을 통해 플라스틱 과립으로 변환하는 것입니다.
보통 2대의 기계(주 기계 1개, 보조 기계 1개)를 준비합니다. 이를 통해 효율성을 향상하고 생산량을 높일 수 있습니다.
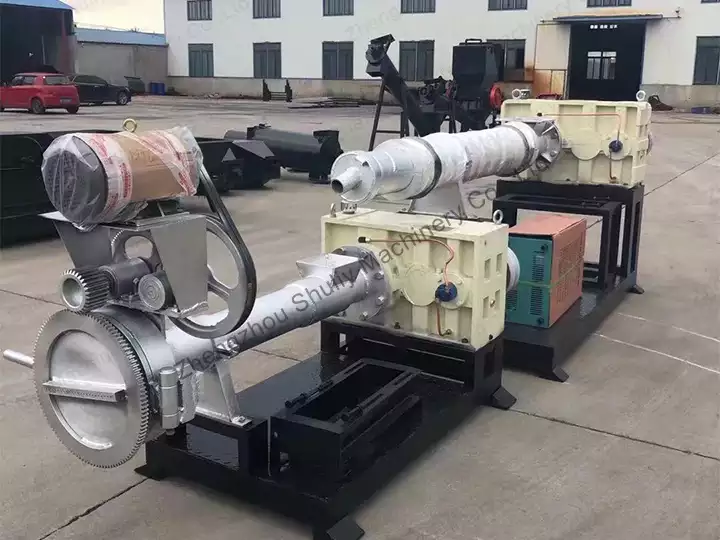
- 용량: 100-500kg/h
- 가열방식: 전자기 가열, 세라믹 가열, 가열 코일
- 압출 플라스틱 크기: 약 3mm
- 소비율: 최대 2%(재료의 더러움에 따라 다름)
- 옵션 장치: 필름재료 강제공급장치
냉각
플라스틱 펠릿 기계로 압출된 완제품은 긴 스트립 모양이며 특정 온도를 갖습니다.
형태와 품질을 확보하기 위해 냉각탱크에 넣어 식혀 굳혀주세요.
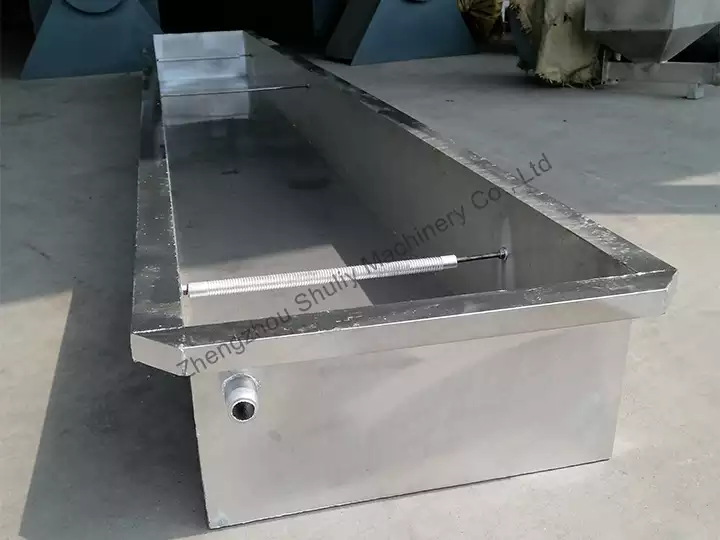
- 길이: 귀하의 필요에 따라 cutomizabla
- 당신은 사용할 수 있습니다 재활용수.
펠렛 절단
냉각 후 펠릿 절단기를 사용하여 플라스틱 스트립을 필요한 길이와 모양으로 자릅니다. 그러면 균일한 플라스틱 펠렛을 얻을 수 있습니다.
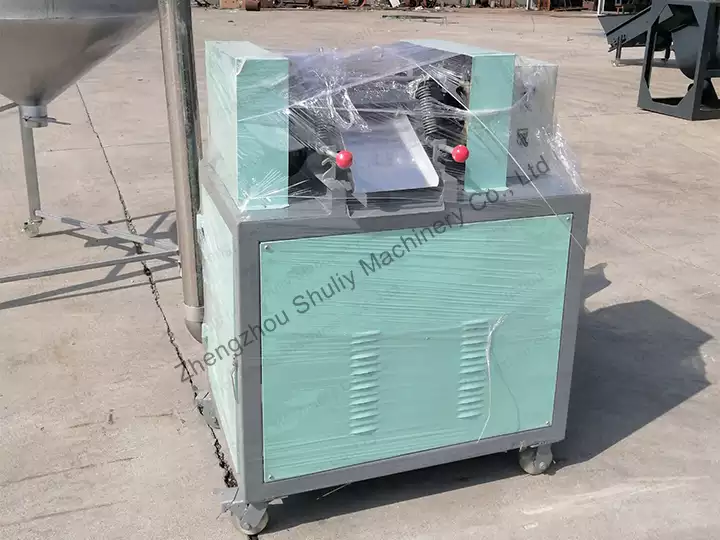
- 입자 크기: 길이 3mm, 직경 4mm의
- 블레이드 소재: 카바이드 호브(플라스틱 과립 2,000톤 절단시 교체)
- 옵션 장치: 진동체(입자의 균일성 및 일관성 확보)
보관 및 포장
마지막으로, 플라스틱 펠렛은 운송 및 판매에 필요한 대로 보관 및 포장됩니다.
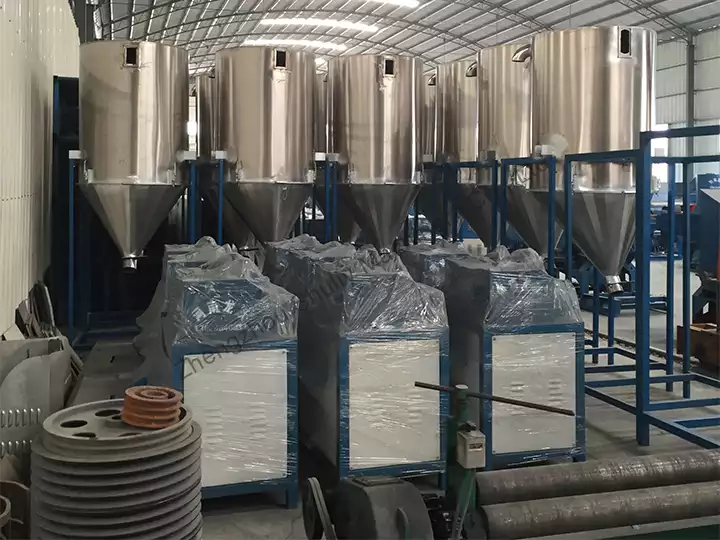
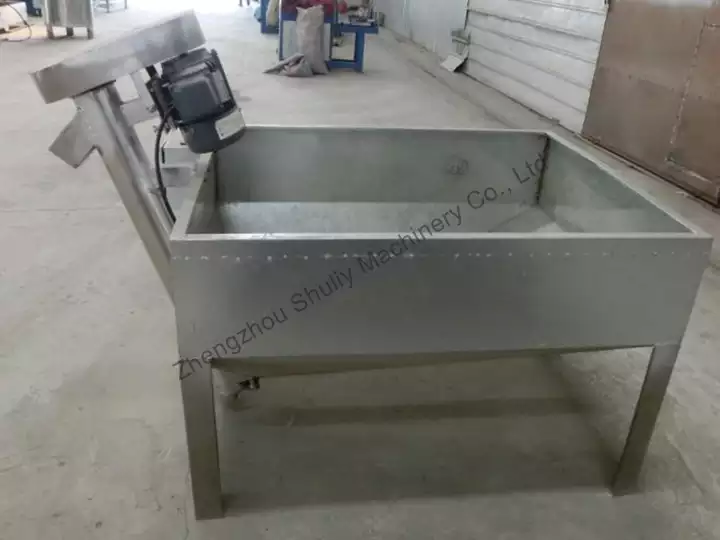
플라스틱 필름과 플라스틱 플레이크 펠릿화 라인의 차이점
다양한 플라스틱 재활용 재료에 따라 우리는 이 라인을 PE PP 플라스틱 필름 재활용 라인과 PE 플라스틱 플레이크 펠릿화 라인으로 나눕니다.
이 두 플라스틱 재활용 라인은 주로 피더와 건조기에서 약간의 차이점이 있습니다.
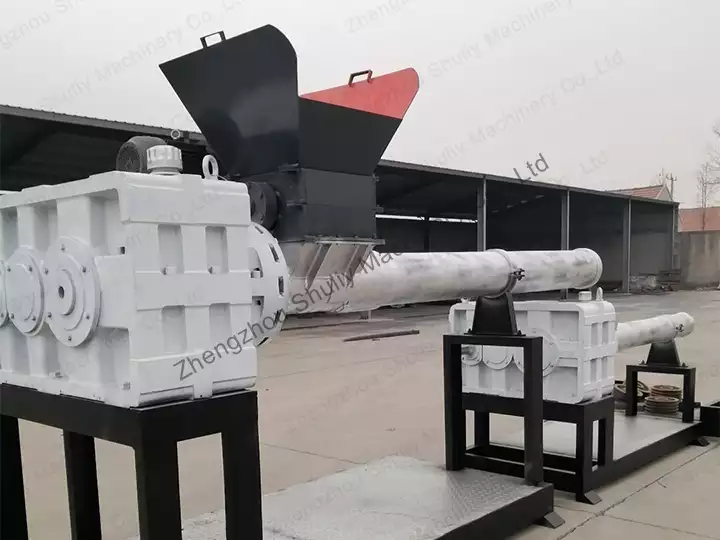
PP PE 필름 세척 재활용 라인에서는 플라스틱 조립기에 강제 공급 장치를 추가해야 합니다.
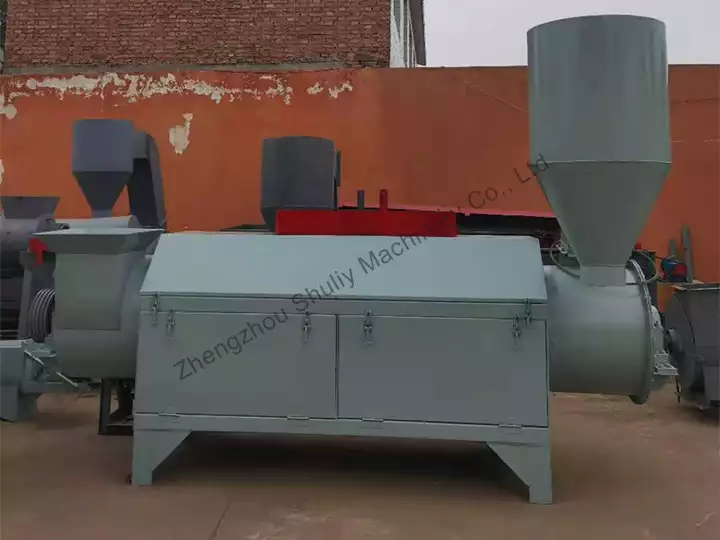
PP PE 플레이크 재활용 라인에서는 수평 건조기를 사용하여 플라스틱 칩을 건조해야 합니다.
판매용 플라스틱 펠릿화 라인의 특징
- 100-500kg/h의 출력. 이 PP PE 플라스틱 펠릿화 라인은 시간당 100-500kg/h의 플라스틱 펠렛을 생산할 수 있어 효율적입니다.
- PP, PE, PVC 및 기타 폐플라스틱에 적합. 이 라인은 다기능이며 경질 플라스틱, 연질 플라스틱 등 다양한 재료를 처리할 수 있습니다.
- 완전 자동화된 운영. 플라스틱 필름 재활용 세척 라인은 첨단 자동 제어 시스템을 사용합니다. 수동 개입을 줄이고 작업 편의성과 생산 일관성을 향상시킵니다.
- 환경 보호 및 에너지 절약. 플라스틱 펠렛 생산 과정에서 장비는 환경 보호 기술을 채택합니다. 이는 녹색 생산 개념에 따라 에너지 소비를 효과적으로 줄입니다.
- 안정적인 펠릿 품질. 플라스틱 재활용 과립화 라인은 압출 및 절단 공정 중에 펠렛의 일관성과 고품질을 유지할 수 있습니다. 생산된 플라스틱 펠릿은 다양한 응용 분야의 요구를 충족할 수 있습니다.
- 저소음 환경. 저소음 설계로 생산 과정에서 발생하는 소음 공해를 줄이고 작업 환경의 편안함을 향상시킵니다.
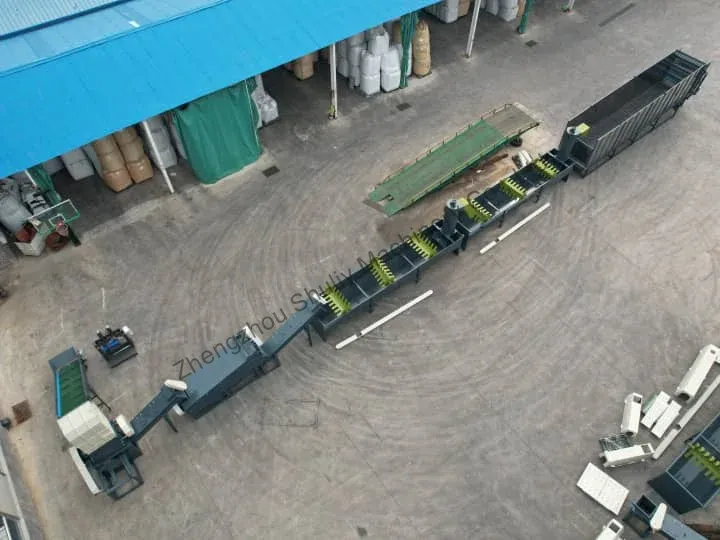
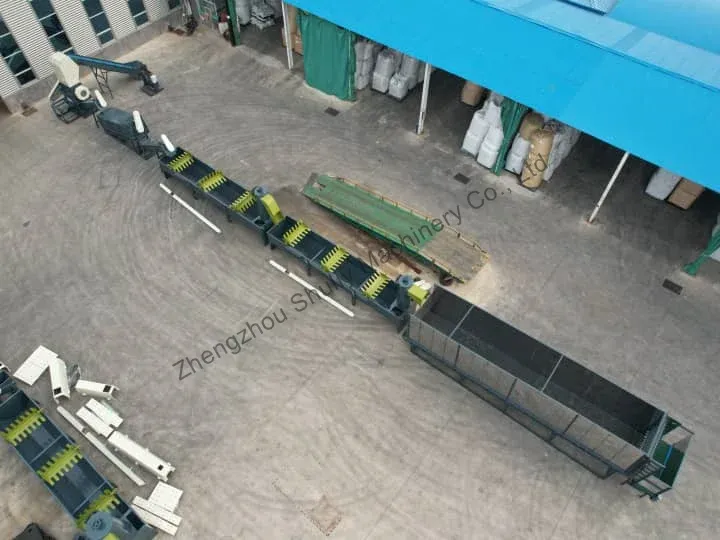
플라스틱 재활용 펠렛화 라인 가격은 어떻습니까?
플라스틱 팔레타이징 라인의 가격은 생산 규모, 생산 라인 구성, 다양한 공급업체 등과 같은 여러 요인의 영향을 받습니다. 가격은 수만 달러에서 십만 달러 이상까지 다양합니다.
플라스틱 재활용 전문 생산 및 공급업체로서 자세히 설명드리겠습니다.
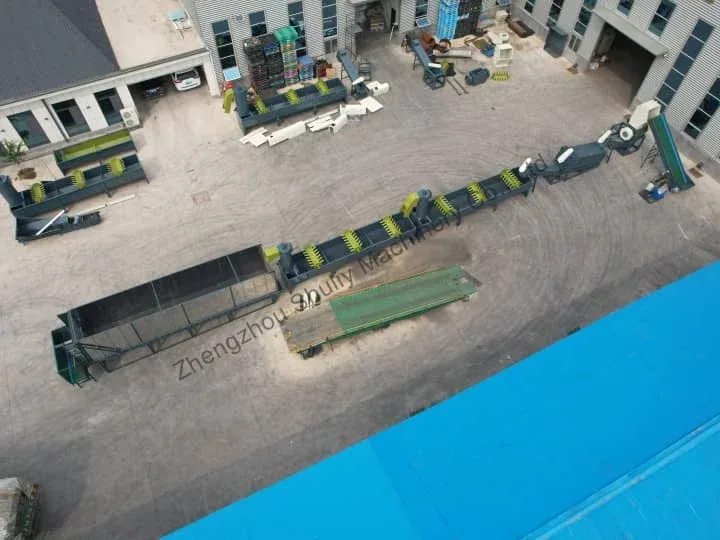
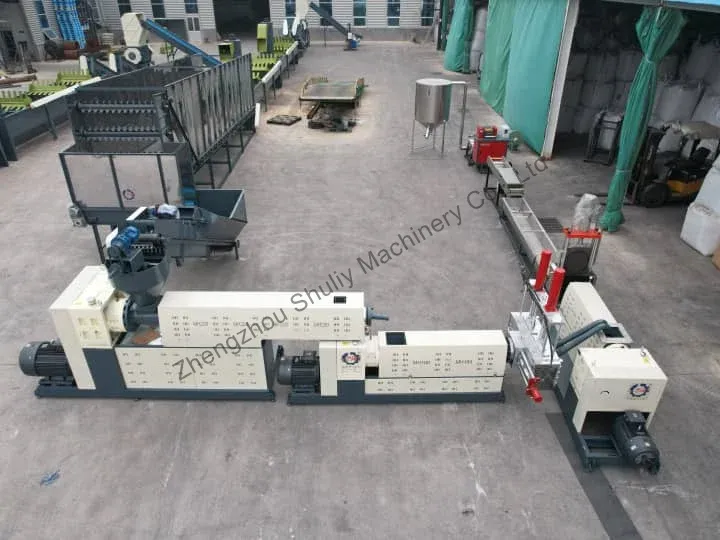
예를 들어, 플라스틱 필름을 재활용하려는 경우 선택할 수 있는 플라스틱 펠릿화 라인 장비는 다음과 같습니다.
컨베이어, 분쇄기, PP HDPE 필름 세척기, 건조기, 강제 공급기, 제립기, 냉각 탱크, 과립 절단기, 보관함, 포장기.
그중에서도 출력에 따라 선택하는 제립기 모델이 다르며 가격 차이도 큽니다. 또한, 보관함 및 포장 기계가 필요하지 않습니다. 수동으로 완료할 수 있습니다. 가격도 다양합니다.
따라서 플라스틱 재활용 과립 화 라인의 가격을 알고 싶으시면 저희에게 연락하십시오. 당사의 전문 직원이 적합한 장비를 추천하고 최상의 견적을 제시해 드립니다.
PP PE 플라스틱 펠릿화 라인 공급업체로 Shuliy를 선택하는 이유는 무엇입니까?
플라스틱 재활용 기계 공급업체가 많은데 Shuliy를 선택하는 이유는 무엇입니까? 우리에게는 다음과 같은 장점이 있기 때문입니다.
- 전문적 지식. Shuliy는 플라스틱 재활용 및 가공 산업에서 광범위한 경험을 보유하고 있으며 효율적이고 신뢰할 수 있는 솔루션을 제공하기 위해 최선을 다하고 있습니다.
- 맞춤형 서비스. 고객의 요구에 따라 맞춤형 서비스를 제공할 수 있습니다.
- 예를 들어, LDPE를 가공하려는 경우 과립화 시 강제 공급 장치를 권장합니다.
- 판매 후 서비스. Shuliy는 장비 설치 및 시운전, 교육, 유지 관리 및 기술 지원을 포함한 포괄적인 애프터 서비스를 제공합니다.
- 품질 보증. 당사의 모든 플라스틱 펠릿화 라인은 엄격한 품질 관리를 받습니다. 우리는 공장을 떠나기 전에 모든 플라스틱 재활용 기계를 테스트하여 안정성과 내구성을 보장합니다.
- 글로벌 고객 기반. 당사의 제품은 전 세계적으로 판매되며 국제 시장에서 좋은 평판을 얻었습니다. 이제 Shuliy 플라스틱 재활용 라인은 많은 고객들에게 인정을 받고 있습니다.
- 원스톱 솔루션. 단일 장비뿐만 아니라 토털 솔루션도 제공합니다.
- 여기에는 프런트엔드 폐플라스틱 처리, 펠릿화 라인 및 백엔드 포장이 포함됩니다.
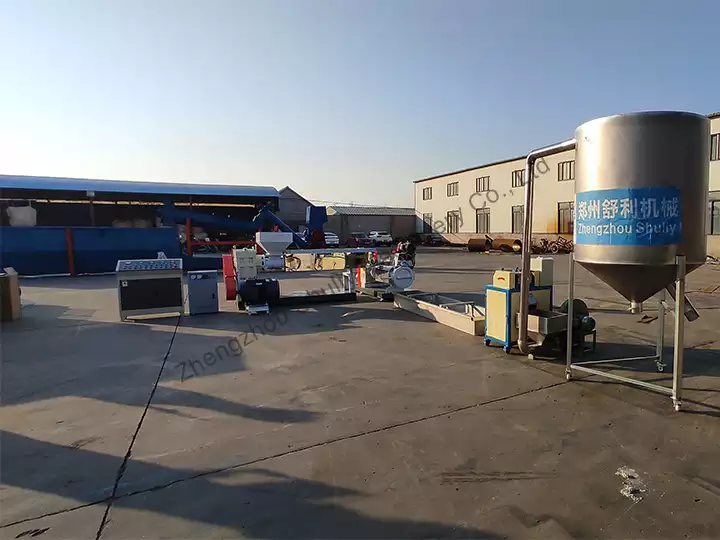
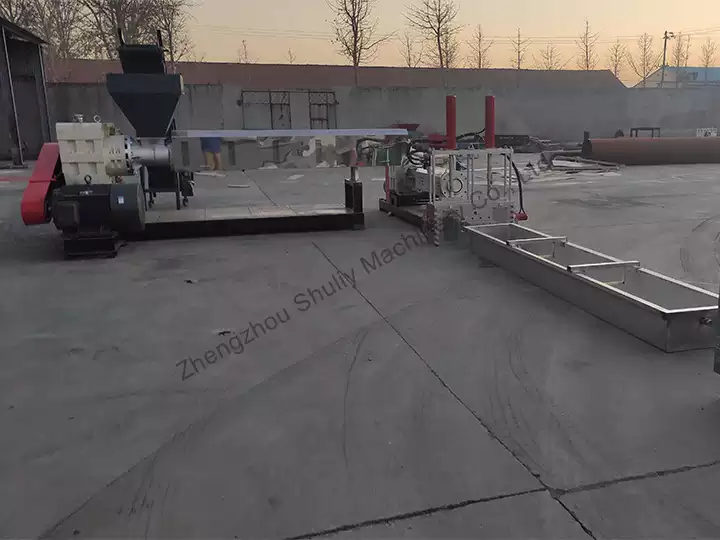
PP PE 플라스틱 과립화 라인 사용 전 안전 점검
- 장비를 정리하고 나사를 확인하고 모든 나사를 조이십시오.
- 배선: 제어 캐비닛의 표시에 따라 모든 모터 와이어, 가열 와이어, 전자기 가열 와이어 및 조립기 와이어를 연결합니다.
- 물 추가: 냉각수 탱크에 물이 채워집니다. 필요한 경우 자체 물 순환 냉각 시스템을 구축하십시오.
- 각 전기 부품의 스위치를 확인하십시오. 모터를 작동시켜 정회전과 후진을 각각 확인하고, 기어박스의 오일 레벨과 회전부의 윤활 상태를 확인하십시오.
- 각 부분의 체결상태를 확인하세요. 전기와 물 공급이 정상인지, 선로와 배관이 잘 연결되어 있는지 확인하세요.
지금 견적을 받아보세요!
플라스틱 재활용으로 이익을 얻는 데 관심이 있으신가요?? 그렇다면 저희에게 연락주시면 전문 매니저가 귀하의 요구에 맞는 최적의 솔루션을 제공해 드리겠습니다.