Fiber carding machine is used in the textile industry and in the field of waste recycling, where the main functions include separating and arranging the raw fibres into parallels, improving uniformity and purity, removing impurities and stains, and blending different types of fibres. It also prepares fibres for subsequent spinning processes, ensuring product quality and productivity.

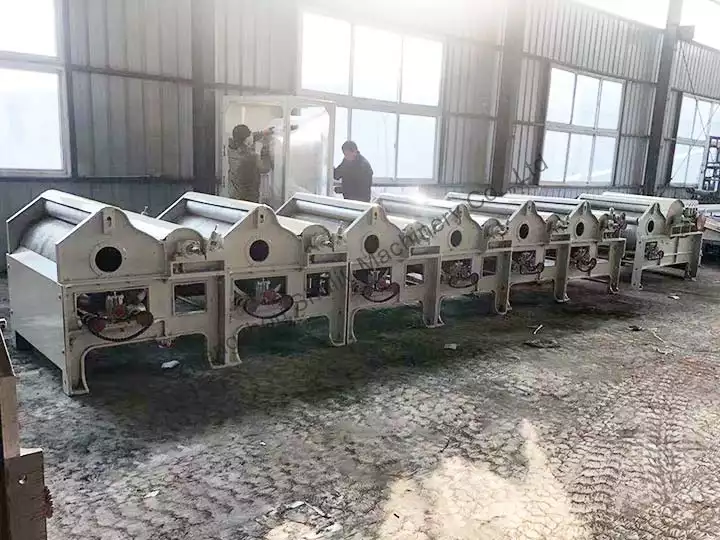
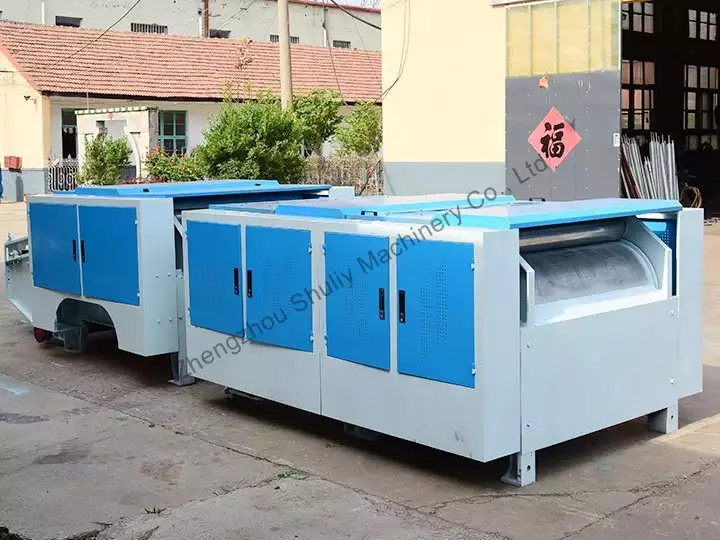
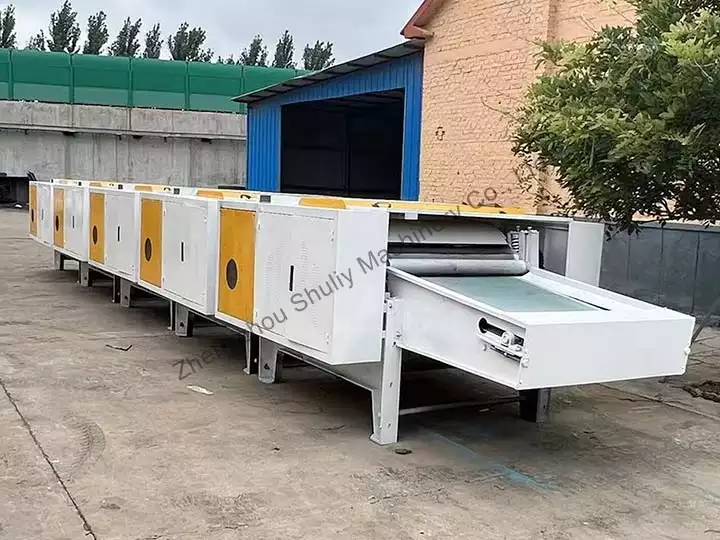
With precise control systems for a wide range of fibre types, this cotton carding machine plays a key role in weaving, spinning and waste treatment. Also, it always works with the fiber opener machine for textile waste recycling.
Features of polyester fiber carding machine
- Efficient carding: able to card and separate polyester fibres quickly and improve production efficiency.
- Versatility: suitable for different types of polyester fibres, such as staple, long staple and recycled fibres.
- Impurity removal: effectively removes impurities, dust and stains to improve fibre quality.
- Precise control: equipped with an advanced control system, carding parameters can be adjusted to meet different processing needs.
- Uniform quality: ensure polyester fibres are uniform and flat during carding, improving the consistency of subsequent spinning and weaving.
- Energy-saving and environmental protection: adopting energy-saving technology to reduce resource waste and comply with environmental protection standards.
- Customized design: provide individual solutions for cleaning machines based on the specific needs of the customer. This ensures that the machine is perfectly matched to the customer’s production process.
Technical data of fiber cleaning machine
Name | Dimension(mm) | Motor(kw) | Roller’s length(mm) | Roller’s diameter(mm) | Weight(kg) | Capacity(kg/h) |
One roller | 2000*1700*1300 | 11 | 1000 | 250 | 800 | 150-250 |
Double roller | 2900*1700*1300 | 29 | 1000 | 250 | 1500 | 150-250 |
Three roller | 4000*1700*1300 | 34 | 1000 | 250 | 2350 | 150-250 |
Four roller | 5100*1700*1300 | 40 | 1000 | 250 | 3200 | 150-250 |
Five roller | 6200*1700*1300 | 45.5 | 1000 | 250 | 4050 | 150-250 |
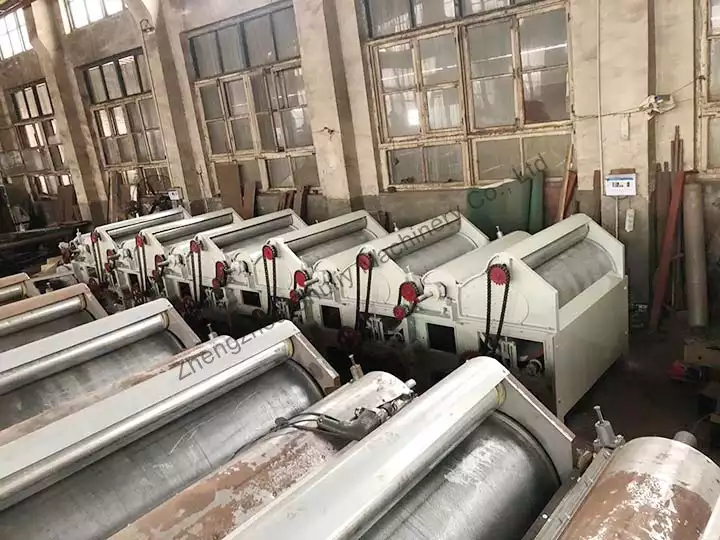
It is important to note that our cleaning machine is often sold in conjunction with the opener to process the textile waste more efficiently. So, if you have a need, welcome to contact us for more machine details!
Applications of fiber carding machine
It is mainly used for cleaning and recycling all kinds of fibres such as yarn head, hemp, cloth head, chemical fibre and so on. And the fiber opener is used in a wide range of applications in several industries, including:
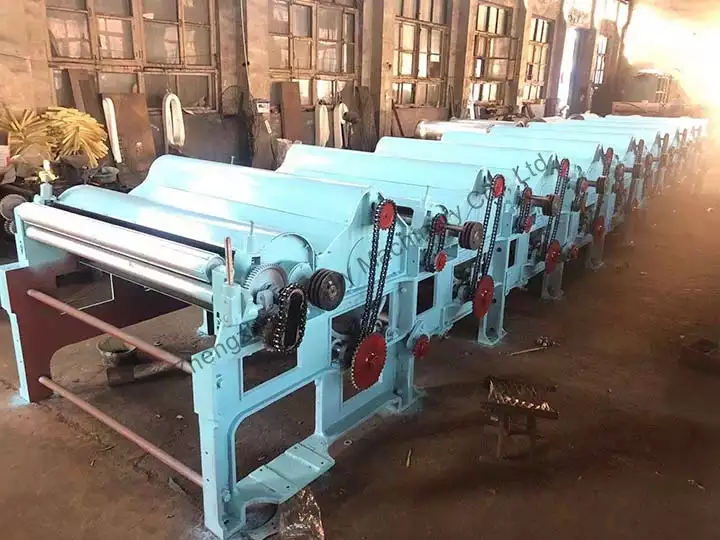
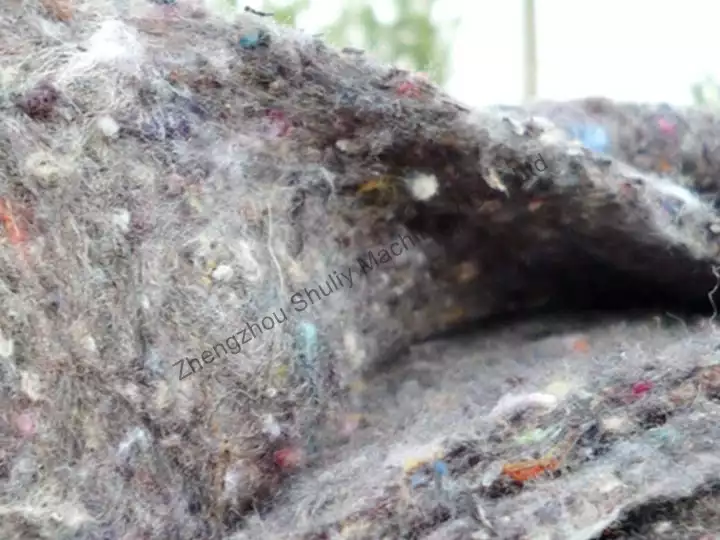
- Textile industry: used to process raw cotton, wool, silk and other fibres to prepare pre-spinning material and improve the uniformity and quality of fabrics.
- Waste recycling: for processing old textiles, discarded clothing and fibre waste, breaking it down, cleaning and preparing it for recycled fibres, supporting sustainable waste management.
- Automotive industry: for the manufacture of car seat padding materials such as car seat cushions and upholstery.
- Filler manufacturing: preparation of filler materials for use in furniture, mattresses, toys and clothing, such as down substitutes and polyester fillings.
- Carpet manufacturing: for processing carpet piles and fibres to improve the quality and appearance of carpets.
Working principle of textile fiber carding machine
The working principle of the cotton carding machine is that the raw material is evenly spread on the feeding curtain, and then sent from the feeding curtain to the two feeding rollers(or even more rollers). And then through the continuous carding and squeezing by the multi-channel spiking rollers, the fibres are constantly loosened and cleaned up, and the impurities are discharged in the process.
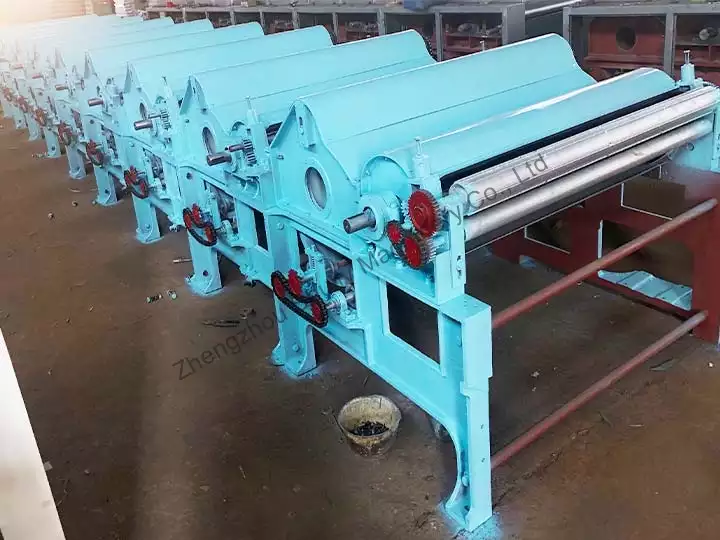
The active fibres are further loosened with the help of the spiking rolls and are finally caught on the surface of the dust collection cage. And then sent out of the machine through the squeezing rotation of the press rolls, ready for collection and baling. This process ensures that impurities are effectively removed from the raw material and the fibres are loosened for improved quality and processability.
What constructs cleaning machine?
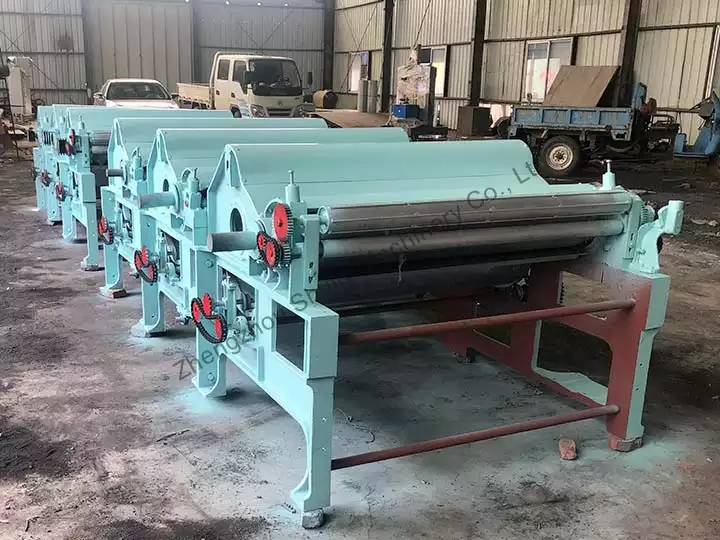
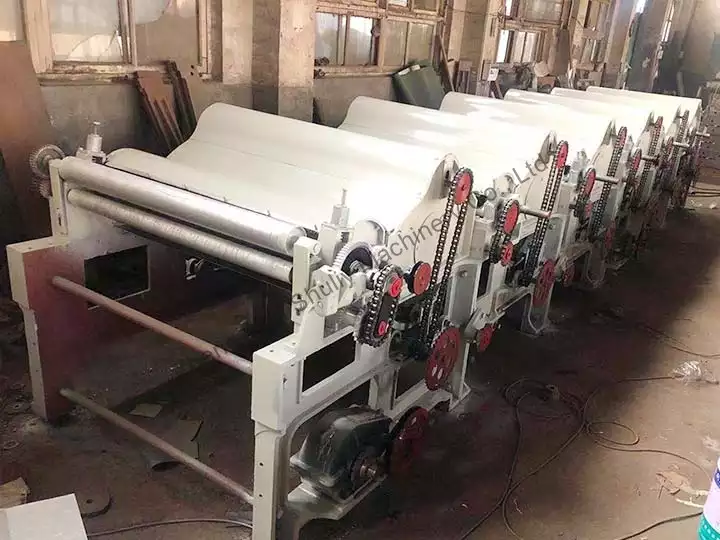
The main components of this cleaner are: frame section, feeding section, flower feeding roller, spiking roller, cotton dust cage, cotton feeding roller section, cotton discharge section, dust exhaust fan, transmission system and so on.
How about the fiber carding machine price?
The price of the hemp fiber carding machine varies according to model, brand, specification and market demand. Typically, larger, higher-capacity, more advanced models are more expensive, while smaller, basic models are relatively inexpensive.
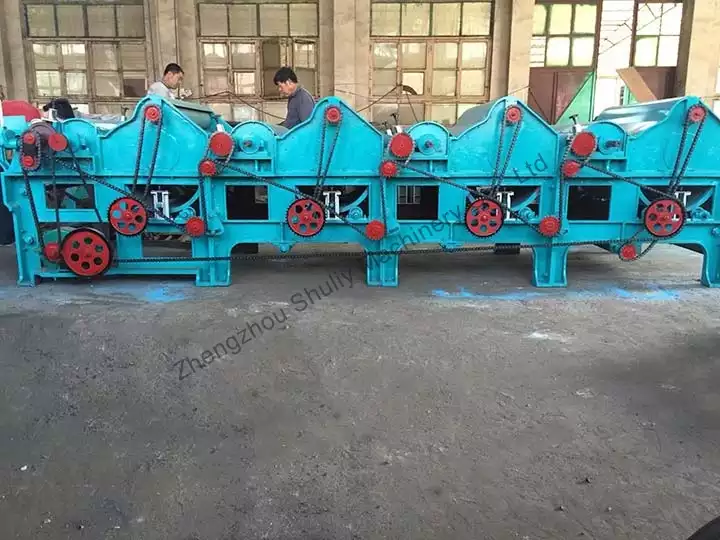
Other costs, such as shipping, installation and maintenance, may also need to be considered when making a purchase about the wool carding machine. For accurate pricing information, it is recommended to get in touch with us and we will provide you with an accurate quote based on your needs.
Safely operate cotton carding machine
- The staff must carefully read the instructions and understand the role of each part of the fiber carding machine and the adjustment method.
- No open clothes, scarves, gloves, skirts, long hair. A helmet is necessary.
- The fiber cleaning machine shall not be placed within one meter around the sundries, processing materials and finished products, and shall not affect the operation, the road should be kept clear, so as not to be hooked by the rotating parts, damage to the machine or injuries.
- During the working process, do not put your hands near the roller to avoid danger.
- Use soft objects such as thin bamboo sticks to clean hanging cotton on the fiber opener machine. It is strictly forbidden to clean directly with your hands.
- The fibre carding machine must be refueled according to regulations to ensure normal lubrication of all parts
- In case of an accident during production, switch off the power supply first and remove the trouble in time.